As one of the critical components of the automobile, the
automobile wiring harness plays the role of connecting the whole vehicle's electrical appliances. When quality problems occur in the wiring harness, it is easy to cause safe throwing, safety, and disaster prevention. As a supplier of wire harness manufacturing and production, in its quality control process, the quality elements covered must be controlled to ensure that the factory quality is qualified and there will be no quality problems using OEM or end customers.
Establish a standardized process for the quality control of the entire vehicle wiring harness so that the
supplier should conduct strict quality control in every link from raw material procurement inspection, online production, and manufacturing to the final product. Warehouse and packaging to avoid receiving or manufacturing. And it will not flow out.
Quality control elements of supplier's wiring harness
1.1 The primary classification of automotive wiring harness
Automotive wiring harnesses are divided into front seat wiring harnesses, ceiling wiring harnesses, instrument wiring harnesses, engine wiring harnesses, and floor wiring harnesses. The front seat wiring harness is the most complicated, with the most branches and the most significant number. Complete functionality.
1.2 Brief introduction of wire harness production process
The primary process: incoming inspection→wire opening→waterproof cover pre-installation→terminal crimping→ultrasonic welding→heat shrink tube treatment→→final assembly→start-up test→visual inspection→storage→transport to the main engine factory.
1.3 Control elements of each process of production and manufacturing
1.3.1 Receipt inspection
In this process, to control the incoming quality of individual parts, the supplier needs to establish a complete internal raw material approval process. A comprehensive, full-function, and full-function verification will be carried out in the approval stage, and sub-suppliers are required to submit a full-performance test report once a year. In particular inspection locations, qualified personnel uses relevant inspection tools (such as push-pull force gauges, vernier calipers, hardness testers, 2D projectors, flame-retardant test boxes, resistance test equipment, etc.) to inspect parts. Such as wires, inspection items include wire diameter, insulation thickness, wire resistance and color, etc.; wiring harness terminals, focus on testing key dimensions, materials, models, appearance, etc.; corrugated tubes, testing flame retardant characteristics and key dimensions; shrinkable heat tubes, inspection The wall thickness, flame retardancy and inner diameter of the product.
1.3.2 Stripping
To ensure the quality and appearance of the terminal after crimping, it is necessary to establish a database that matches the length of the stripping head and the corresponding terminal before crimping. For the size and appearance of the peeling head after peeling, the first and last inspections are required, and records should be kept. The phenomenon of incomplete peeling of the diagonal cutting blade and the blade is not allowed. It is not permitted to strip wires with a diameter of less than 1.5mm2 to damage the copper wire, and wires with a wire diameter of more than 1.5mm2 are allowed to deny less than 8% of the copper wire.
At the same time, semi-finished products should be stored and transported in a suspended manner and must not be stacked or mopped. After the stripping is completed, the wires should be bundled in a certain number. At the same time, special tools and protective equipment must be used for protection, such as wire protection cups, wire protection sleeves, etc. It cannot use plastic wrap, plastic bags, plastic paper cups, and other very likely items to cause damage to the iron core. As the first process, stripping plays a crucial role in later quality.
1.3.3 Pre-installed waterproof box
Choose a waterproof jacket that matches the diameter of the wire. Before assembling, the waterproof jacket must not have flying wires, copper wires broken, and copper wires tightened. After assembly, the waterproof box can't loosen or fall . The waterproof jacket acts as an insulation and prevents water ingress in the entire wiring harness, ensuring that the waterproof jacket is in place.
1.3.4 Terminal crimping
①Mold management. The crimping mold must accept the profile acceptance and be equipped with enough spare parts to prepare for the fragile crimping jaws. The mold must be inspected every day before use, and the mold and crimping tool must be recorded in the inspection account, and the record should be visible. The history includes the number of times the mold is used, the number of times the jaw is used, the maintenance information of the jaw and the decay, maintenance information, replacement information, etc.
After using the mold, the mold should be cleaned up in time, and the information should be stored in the ledger. After entering the warehouse, it should be customized according to the location, so please use a softer item to protect the jaws to prevent damage. It is worth noting that after the production is completed, the final crimped sample of the terminal should remain on the mold.
② Process control. Choose to use pneumatic mold (automatic or semi-automatic) to ensure that the
wiring harness terminal is placed in the correct position during the feeding process, and the consistency is good, and the quality requirements are met. Terminal crimping needs to ensure the ability of personnel and the stability of the equipment. So, it is necessary to train terminal crimping personnel in advance, improve the skill of operators, and conduct evaluation and evaluation to improve the consistency of crimping production. At the same time, equipment CPC analysis is also required, and the data is more significant than 1.67, indicating that the process is stable. Figure 1 is a schematic diagram of terminal crimping.
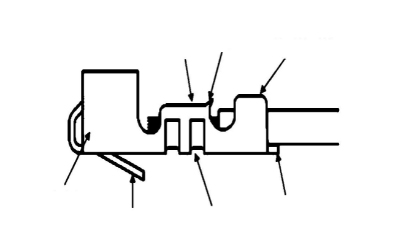
For the storage of semi-finished products afterward, quantitative binding and hanging methods are adopted, and they cannot be stacked. Clarify the routine inspection items to be performed after terminal crimpings, such as terminal crimping height and width measurement, pull-out force measurement, terminal profile inspection, contact voltage drop inspection, visual inspection, etc.
1.3.5 Ultrasonic welding
Ultrasonic welding needs to provide clear operating instructions for each process to specify standardized operating procedures to guide employees in operation. The equipment setting process parameters must also be in charge of full-time personnel, such as welding temperature, welding time, cooling time after welding, dimensions after welding, etc. At the same time, confirm the above parameters and record them as the content of daily inspection. Welding equipment must be equipped with pressure monitoring devices to identify defects such as missing wires and poor insulation. The following problems are not allowed after welding, such as flying leads, bending of copper wires, etc. As shown in Figure 2, it is necessary to measure and record the length and tension of the exposed copper wire at both ends after welding. At the same time, the difference between the wire diameter of the welding wire used in ultrasonic welding must not exceed 1mm2.
1.3.6 Heat-shrinkable tube treatment
It is forbidden to use the heat gun to process the heat-shrinkable tube . Crawler and reciprocating heat shrink machines must be used. At the same time, the machine parameter settings must match the specifications and models of the heat-shrinkable tube. The parameters of the heat-shrinkable tube assembly process control need to be set : such as temperature, time, appearance, and other requirements. After heat shrinking, do not have the following problems: copper wire leakage, insufficient glue, damage to the wire skin, and copper wire piercing the heat-shrinkable tube. The heat-shrinkable line is a kind of protection for the wiring harness, so it must not be damaged. During the transfer process, care must be taken that the tool metal must not be exposed and must be covered.
1.3.7 Pre-installed
When arranging the production line, a process area should be set up near each final assembly line for smooth assembly. When making, special pre-installation tools must be equipped. Before pre-installation, please check the jacket model and wire type specified in the process description document, check the crimp quality of the jacket, wires, and terminals, and pay special attention to the blind plug components of the waterproof plug-in. For the sheath's pre-installation, the sheath's length and color must be checked, and the sheath cannot be misused.
1.3.8 Final Assembly
The manufacture of the
harness assembly tool board ensures the accurate positioning of the connectors, buckles, and accessories, and the accessory model and assembly direction are reflected on the tool board to ensure that the operator can actually install the cable ties and pins during the operation process. Modules that provide effective error prevention. When tying the straps, employees must ensure that they are in the correct position.
After binding, the cable tie cannot be moved. The tail of the cable tie maintains a speed of 3 to 5 knots, and the cut is smooth. When winding with a corrugated tube, before fixing the corrugated box, the wire must be wrapped around the two ends of the corrugated pipe with tape 3 to 5 times. After the dressing is completed, the bellows must not fall or shift. Raw materials and semi-finished products need to be stored at a fixed point. The height of the wireframe of the workstation should be determined according to the length of the semi-finished product, and the phenomenon of terminal landing and material accumulation is not allowed. For buckles in critical positions, self-inspection and marking are required. For products with branching directions, the drawing version information must be reflected on the tool board at the same time.
1.3.9 Boot test
The continuity test bench for production equipment is shown in Figure 3. The items to be tested include electrical performance, water resistance, airtightness and continuity of the plug-in, whether the direction is correct, and whether the plug-in secondary self-locking has been assembled. In place, whether the terminal is returned, etc. The inspector of this process needs to set the designated personnel and personnel authority. Inspectors should be trained and tested and then work after passing the assessment. During the continuity test, all plug-ins must be placed in a normal and natural state after being connected, and the plug-ins cannot be squeezed by professionals. Before and after the operation, the sensors, probes, and test modules in the conductivity meter must be checked daily. Problems such as probe deformation, non-rebound, and damage to the test module are not allowed. When this problem occurs, please report it to the corresponding management and maintenance personnel in time.
1.3.10 Visual inspection
It is necessary to set up a dedicated inspection area, plan the area to be inspected, the area of qualified products and non-conforming products. Set up the seal sample or wiring harness data map on-site, a 1:1 large map (the drawing version information needs to be reflected). It is consistent with the version number of the assembly tool board and the connectivity test station. The inspection content of this process includes: comparing and confirming whether the plug-in model (different configuration) is installed and used , whether each plug-in terminal is damaged, whether the accessories are missing, whether the color of the wire and the wire are correct. Whether the diameter is suitable, whether the strap is firm, whether it is twisted, whether the spiral pattern of the protective tape is correct, whether the connector is qualified, etc. After the inspection is completed, stamp the label that passed the electrical inspection for confirmation, paste it on the product, and place the qualified product on the turntable equipment.
1.3.11 Storage
When entering the area, you need to pay attention to ventilation, humidity, and electricity and control the temperature and humidity when necessary. The finished product warehouse area should be set
● Storage areas: storage area
● Storage parts, storage area
● Storage parts, storage area for unqualified details, and storage area for
Qualified parts. Read labels are used for incapable parts, yellow tags are used for slow parts and test parts, and green labels are used for suitable parts. At the same time, batch management is needed, and a batch management system is used to realize the first-in-first-out management requirements of parts .
2 concluding remarks
There is no doubt that the
wiring harness plays a vital role in the vehicle system. Due to its complex production process, each production process should be paid attention to. Don't pursue progress, but identify and control the elements of each method. Only this article will show the central control elements of each process or procedure so that the supplier can better meet the quality control requirements.